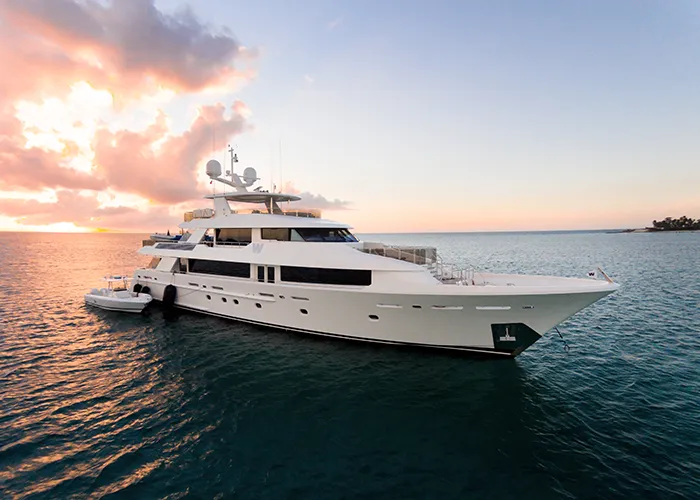
About Westport
Westport Yachts, a premier builder of American-made luxury yachts, turned to advanced manufacturing to replace traditional tooling methods. The company specializes in both custom and model-line all-composite yachts. Westport exclusively builds all hulls and major deck parts in one-piece, precision-engineered molds to ensure structural integrity and resistance to stress.
Drivers for Change
Historically, Westport constructed tooling in-house using conventional hand-lofting techniques. This process required highly skilled labor and extensive finishing work. In response to rising labor costs, compressed build schedules, and a need for higher precision, Westport partnered with Janicki Marine.
Janicki supplied directly machined, one-off tooling to cast primary composite components, including hulls, decks and superstructures. This marked a shift from legacy craftsmanship to high-tech, lean manufacturing.
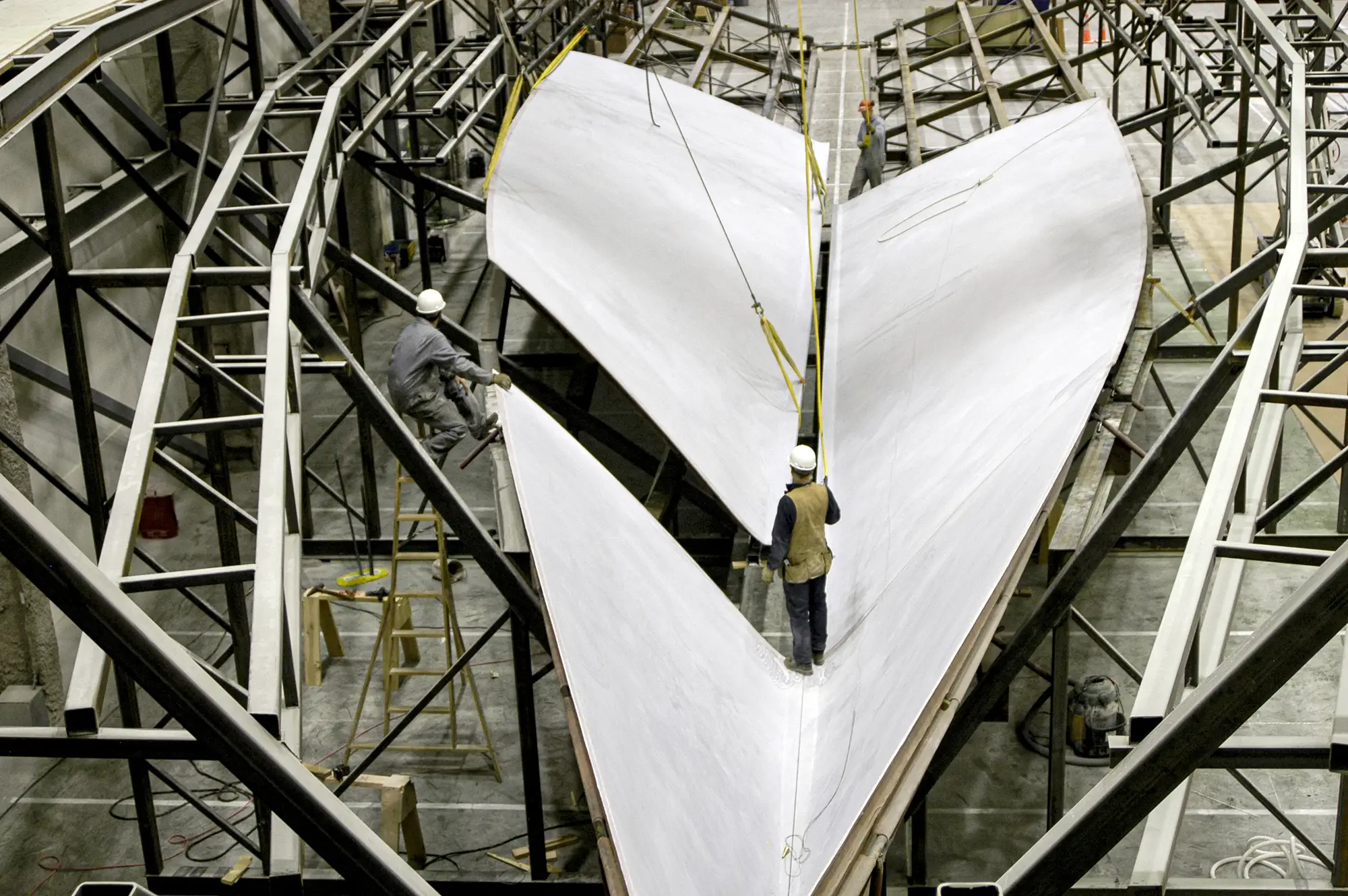
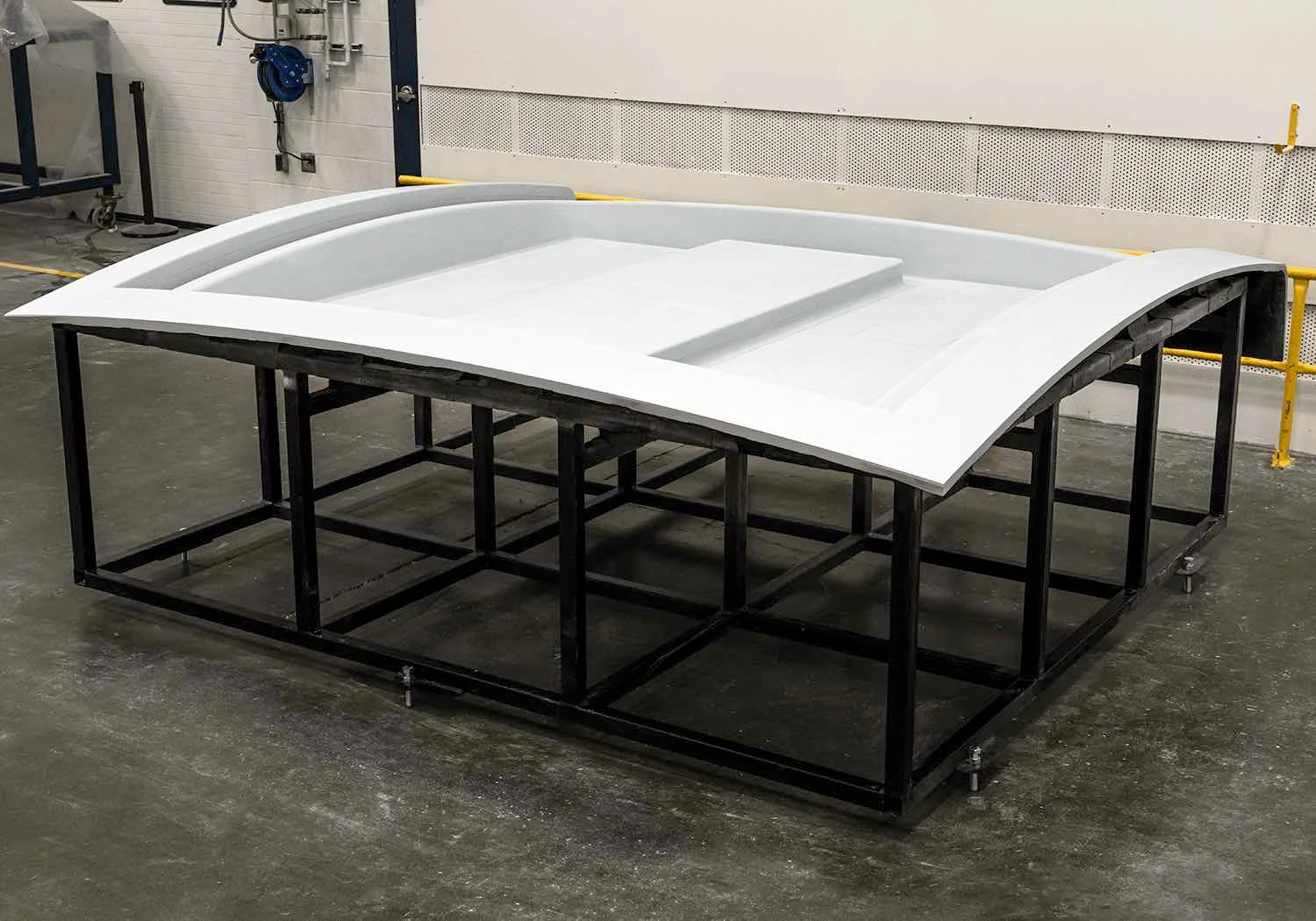
Tooling Redefined
Janicki delivered highly accurate, vacuum-tight tooling with shorter lead times. This improvement was crucial to enhancing Westport’s production efficiency and product quality. The tooling featured proprietary building materials and state-of-the-art 5-axis machining processes to ensure both structural integrity and manufacturability.
Key challenges included maintaining material stability and designing robust tooling structures. These were overcome through innovative engineering and manufacturing techniques. Compared to legacy methods and alternative vendors, Janicki’s proprietary materials and equipment offered clear performance advantages.
“Whether large or small, the quality of the tooling has been exceptional and is typically ready to produce parts,” said John Wallin of Westport LLC.
Results That Set Sail
In addition to reducing skilled labor costs, Westport realized several benefits from the collaboration:
- Improved vacuum integrity, structural strength and geometric accuracy.
- A significantly reduced production schedule.
- Enhanced integration of tooling with downstream custom modifications.
An unexpected benefit was the ease with which Janicki’s directly machined tooling integrated into Westport’s existing production systems. This compatibility supported efficient, bespoke modifications for each yacht.
Janicki’s ability to combine cutting-edge machining technology with proprietary materials and a responsive engineering team established the company as a key strategic partner for Westport.
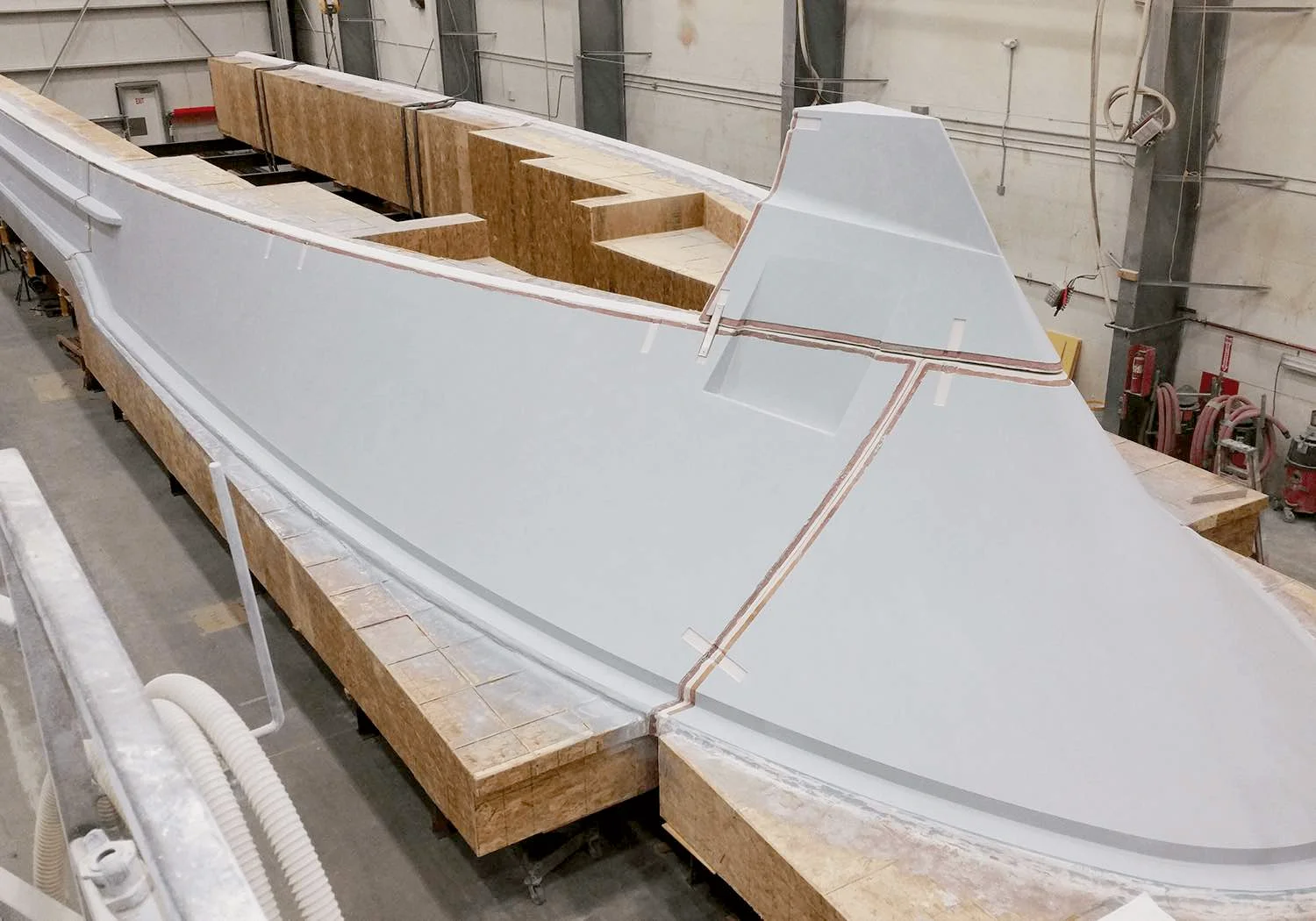